When choosing a linear actuator, it’s important to figure out which drive train is best for your application.
At Rollon, our engineers manufacture linear actuators with three different drive train options: belt, ball screw and rack-and-pinion systems. Each comes with numerous factors that can help you determine the most efficient drive train system.
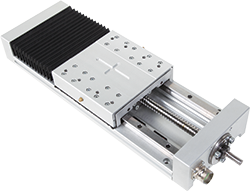
Repeatability and precision
Accuracy refers to the repeatability and precision of the drive train. Our ball screw-driven actuators offer accuracy ranging from ± 3 to ± 50 microns. This is possible due to the precision ground nature of a ball screw system that’s usually offered in a preloaded ISO 5 precision standard. Our rack-and-pinion systems have a level 7 or 8 quality and repeatability of ± 50 to ± 250 microns. Belt-driven actuators follow at a precision range of ± 50 to ± 100 microns.
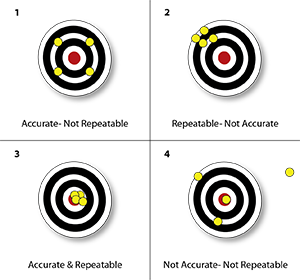
Output force
Capacity refers to the output force that each of the three different systems offer. Since the system is composed of the ball screw, a ball nut and recirculating ball bearings, ball screw systems offer the most output force. Our ball screw actuators can output forces up to 13,100 pounds. Rack-and-pinion systems can offer about one fifth, or 20%, of this and belt systems are limited due to the stretching nature of polyurethane to about 3/20, or 15%.
Travel
As far as travel is concerned, our rack-and-pinion system can be joined for applications that require motion in excess of 100 feet. Belt-drive systems are limited to between 20 and 40 feet before belt-sag becomes a serious issue. Ball screw systems can experience possible failure due to whip effect so they’re restricted to lengths of about six feet.
Our engineers size all drive trains based on usage, and always suggest external sealing or protection if they’re going to run into any washdown or flying debris contamination.
Shipping
We manufacture and ship belt systems within 3 to 4 weeks, ball screw systems within 4 to 6 weeks, while rack-and-pinion systems take between 8 to 12 weeks. Both systems work well in vertical applications where customers are concerned with belt sag. Our SC and S-Smart systems incorporate idler pulleys to counter this phenomenon in vertical applications. Rollon belt and rack-and-pinion systems have a maximum velocity of five meters per second. Ball screws are limited in their rates of speed due to the whipping nature of the system to about one meter per second.
Check out a recent white paper for further tips about specifying and sizing your actuator.